While today's cars have a lot of bells and whistles, you can be a bit hard pressed to find all the features that you want in your vehicle (at least not without blowing your budget).
This project was born from a need to address a couple of features that I wanted to have in my truck.
The first feature was to have an electronic compass to serve as a companion to my 2 meter amateur radio rig. As a severe storm spotter, knowing what the direction is of the weather that I'm observing is essential for when I need to radio in my reports.
The second feature is more along the lines of creature comforts. Many vehicles these days have an outside temperature read out feature, however you very rarely find one that will display what the temperature is inside the vehicle. I always wanted to know what the actual temperature is in the car when I'm driving (and it's a great help in solving those age old debates that you sometimes have with your passengers on whether it's "too hot" or "too cold" )
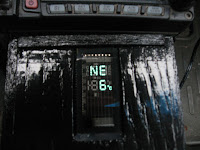

By utilizing one of these displays, I determined that I would probably be able to build a standalone compass and interior thermometer. As an added bonus I wanted to it built in such a way that it could be be easily moved from car to car (or really to any "mobile" object, like a boat for example).
Step 1: Finding the Donor
Compass and outside temperature displays are actually fairly common features that are found installed in the center overhead consoles in many minivans that have been produced over the past couple of decades. The unfortunate thing about those particular temperature displays is that often the outside temperature sensor is fed into the vehicle's' ECM module where it's used to provide input for other vehicle functions (like running the cooling fans) with the console reading the outside temperature data from the ECM. I considered this to be a bit too complex of a thing to tackle for what I had in mind.
There are however a number of vehicles that utilize the rear view mirror to display the compass heading and outside temperature. These mirrors, generally manufactured by Gentex, are more commonly found in GM SUV's.



The outside temperature sensor that is used by the mirror is located in front of the radiator of the vehicle and is attached in the middle of the bottom radiator mount. To get at the sensor, you need to remove the top part of the front grill of the vehicle to expose the front of the radiator. In the case of the Vue, this means removing 2 plastic speed nuts in the center of the grill and pulling back on it to expose the radiator and the sensor.
The sensor itself is also attached to the radiator support by a plastic speed nut. To remove the sensor, Remove the speed nut by gently prying up on it with a flat screwdriver until the sensor is free. Once the sensor is free, cut the wire that is attached to the sensor (again, make sure to leave some wire attached to the sensor for later on).
Step 2: Gathering the Parts
After the trip to the junkyard, you should have the following pieces:
- The rear view mirror
- The compass sensor (Attached to the windshield mount for the mirror)
- Wiring harness for the mirror
- Outside temperature sensor (including wiring harness for the sensor)
Before we go any farther, now would be the time to do a quick "smoke test" to ensure to that the mirror and the temperature probe are working as expected - After all we did get our parts from a junkyard.
The wiring harness for our mirror has 5 wires:
- A Yellow wire - which is the the 12 Volt Positive wire
- A Black wire which is the 12 Volt Ground wire
- A Light Green wire which is used for back up lamps - we will not be using this wire
- A Light Green with Black Stripe wire which is used for the temperature probe
- A Grey wire which is used for the temperature probe


Unplug the wiring harness from the mirror by depressing the tab on the plug that's attached to the wiring harness and pulling it out of the mirror. Once the wiring harness is removed, remove the plastic wrapper that is covering the wires on the harness. Cut the Light Green wire (not the Light Green with Black Stripe wire) at the base of the wiring harness plug.
The wire to the compass sensor can be left plugged into the display circuit board
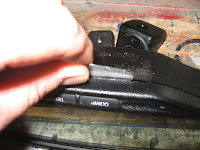

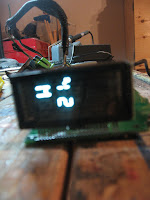


Step 3: Building the Case - Cutting the Sides
The next step is to construct a case for the compass/thermometer. Based on the measurements of the display circuit board that's being used, I needed to build something that would be roughly 3 inches high, 3 inches wide and about 7.5 inches long.
While you could try different case configurations based on your particular needs, since I was going to have the compass/thermometer as a companion for my 2 meter radio, I determined that a simple "box" which would sit on the floor of my truck beside my radio would be the best solution for what I wanted to accomplish..
To build the case, you need the following:
Materials:
- 4 pieces of 3.5" X 7.5" 1/2 inch plywood for the sides of the case
- 2 pieces of 3" X 3.5" 1/2 inch plywood for the front and back of the case
- Wood Glue
- 1 inch finishing brad nails
- Paint
- 12 Volt Power socket - I picked mine up at my local surplus store - but you can pick them up at any electronics supplier
- 12 volt automotive power cable with connector to match the power socket
Tools:
- Table saw
- Miter saw
- Scroll saw
- Drill with a 1/2 inch and 1/4 inch drill bit
- Hot Glue Gun and Glue Sticks
- Soldering iron and solder
- Router and router table with a 3/4 inch straight router bit
- Nail gun (air powered preferred)
- Clamps


Start by making the sides of the case. Using a 3.5 inch by 30 inch section of 1/2 inch plywood (You can this piece of wood from a larger piece of plywood by using a table saw if required), cut out four 7.5" pieces of plywood with a miter saw.
Once you have your four 3.5" X 7.5" plywood sides cut, Set up your router with a 3/4 inch straight bit. Set the router depth so that the bit will cut a 1/4 inch X 1/4 inch edge. Once you have set the router to cut at the correct depth, Cut a 1/4 inch X 1/4 inch groove along all edges of the four plywood pieces (A word to the wise - make sure you cut the 4 grooves on the same side of the plywood!)
By cutting these grooves along the edges, you are actually creating half lap joints that will be used to assemble the case later on. The main reason that I chose this method was that I wanted the joints for the case to be as simple but as strong as possible (If you don't have a router, or if you rather go much more simpler, a simple butt joint will work fine too).
Test fit the sides by assembling the 4 sides together into a box. The grooves should interlock together to make tight fitting joints.
Please take note of the cutting and routing diagrams in the photos above, we will also be referring to them in future steps.
Step 4: Start Building the Case


To get some guidance on how this will be done, just refer to the routing diagram in the previous step, (but never fear - we'll walk through the steps on mounting the circuit board)

With a table saw, set your blade depth to 1/4 inch and set your saw fence to be 1 inch in from the blade. Cut a 1/4 inch deep groove on the top and bottom pieces of the case along the the lines that you've just marked.
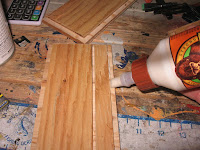

Step 5: Creating the Front of the Case


After that, use the router to cut a 1/4 inch X 1/4 inch edge along the four sides of both plywood pieces (this would be similar to what was done for the side, top and bottom pieces in the previous steps).


Once you have the opening for the display marked out, cut the opening out of the front of the case with a scroll saw. Make sure to give the opening a test fit with the LED display and make any required adjustments so that the display can snugly fit the opening.

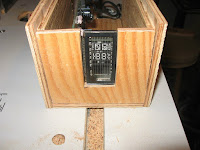
Step 6: Creating the Back of the Case
We now focus our attention on the back part of the case.



Once the groove has been cut, do a final test fit of the display circuit board in the case. With the front and back plywood pieces of the case installed The circuit board should fit snugly into the slots that have been cut into the front and the back pieces.

Step 7: Creating the Top of the Case
Now on to the final part of the case - The top!
In a previous step we had put in a 1/4 inch groove in the inside of top of the case. However during a test fit with the display circuit board I noticed that some additional clearance is needed in the top to allow access for the power connector on the circuit board.


bottom of the case.
Step 8: Putting It Together
Now that we have all of our parts of the case cut and configured so that the display circuit board can live happily inside it, it's now to put everything together.
To assemble the case, start by attaching the front and back of the case to the main body of the case . Attach the front and back by applying a little bit of wood glue along the inside grooved edges of the bottom and sides of the case on both the front and back ends of the case body. Firmly seat the front and back pieces into the case body. Make sure that the grooves that you routed in the front and back pieces for the display circuit board line up with the groove that you cut in the bottom of the case. Also make sure that the opening that you cut for the LED display on the front piece is pointed towards the top of the case.
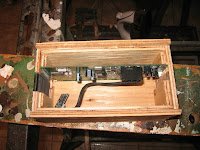
Once the glue has dried, it's probably wouldn't be a bad idea to give the display circuit board one last fitting to ensure that it fits properly in the case (if you need to make any fine adjustments at this point, you can make them by using with some course sandpaper)

On the right side of the case, drill a 1/4 inch hole towards the back end of the case, near the bottom of the case. This hole will used as the access port for the power connector for the display circuit board.
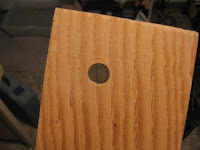

Step 9: Installing the Display Circuit Board
Now that the case is all assembled and painted, the time has come to permanently install the display circuit board.,
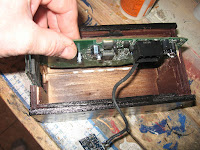


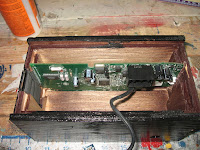
The display board is now installed in the case. Allow the glue to dry fully before moving to the next step.
Step 10: Wiring It Up
It's now time to connect the various components together to the wiring harness.
The first step is to wire up the power connections. Taking the 12 Volt power socket, connect the yellow wire on the wiring harness to the positive terminal of the socket followed by connecting the black wire on the wiring harness to the negative terminal of the socket.


After all the wiring connections are done, mount the 12 Volt Power socket into the case. Apply some hot glue to the outside of the power socket (make sure not to get any hot glue inside the the electrical connections of the socket). and insert the power socket into the 1/4 inch hole that we previously into the side of case.


Plug the plastic connector of the wiring harness into the display circuit board and we are all wired up!
Step 11: Installing the Compass Module
Now that the display circuit board secured into the case, we now need to attach the compass sensor to the case.
Where you place the sensor within the case will depend on how the compass/thermometer is going to be mounted in the vehicle. For the compass sensor to read properly, the sensor circuit board needs to situated horizontal to the ground, with the end of the sensor that not have the cable that goes to the display circuit board connected to it pointed in the direction that you would be traveling (or inversely, the end of the sensor that has the cable attached would be pointing to the rear of the vehicle)
In my case, the compass/thermometer is going to be located on the floor of my truck with the display pointing upwards. So as a result, the compass sensor is going to be attached to the back of the case, with the side of the sensor that has the cable connection pointing towards the bottom of the case (or to confuse further... pointing towards the rear of the truck :) ).
If your compass/thermometer is going to be sitting on top of your dashboard, you would need to place the sensor to the bottom of the case with the side of the sensor that has the cable connector pointing towards the LED display.
Once you've determined where to place the sensor, secure the sensor to the case with some hot glue.
Step 12: Attaching the Temperature Sensor
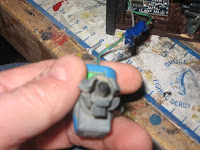
Therefore, installation of the sensor is very straight forward. Just insert the probe end of the sensor into the hole and secure it with a bit of hot glue.
Once the glue has dried on the sensor, fit the top of the case onto the body of the case
In order to allow for future access to the display board if any future adjustments are needed (you'll see why in the next step), do not glue the top onto the case. The top should fit snugly into the case without any fasteners, however if the top doesn't fit very snugly, you can always use double sided tape to secure the top.
The junkyard compass/thermometer is now assembled and ready to try out!
Step 13: Vehicle Installation and Calibrating the Compass
Take the compass/thermometer out to your vehicle and plug in the 12 Volt cable into the compass/thermometer and into the 12 Volt power socket of your vehicle. Make sure that you power being applied to the socket.
The LED display should light up and show a "meaningful" compass heading and temperature. At this point we should do a calibration of the compass in order to make sure that the compass is as accurate as possible.


The compass is now in calibration mode. The easiest way to calibrate the compass is to basically just go for a drive. When driving, make sure to make one or two circles, usually a couple of drives around the block will do it. Keep in mind - very tight circles won't work (So... No donuts in a parking lot!). The idea is that you want to point to all points of the compass.

Step 14: Time to Hit the Road
The compass is now ready to point you in the right direction while at the same time letting you know exactly how hot (or cold) you are.
In my case the compass/thermometer compliments my 2 meter amateur radio rig quite nicely. However the nice thing is that since that it is completely portable, it can be easily moved from location to location. So for example, when I'm not storm spotting, this will be quite a handy accessory to have in the boat this summer while I'm out fishing.
Why not give it a try for yourself and never be truly lost again!
No comments:
Post a Comment